
A recent McKinsey survey revealed that 44% of respondents have moved to regional sourcing in the last year, and more than half expect that trend to continue. In response to recent disruptions, supply chain leaders are changing their strategies. Using JIT sensibility instead, you would send the model to a regional manufacturer that can turn it around in a fraction of the time.
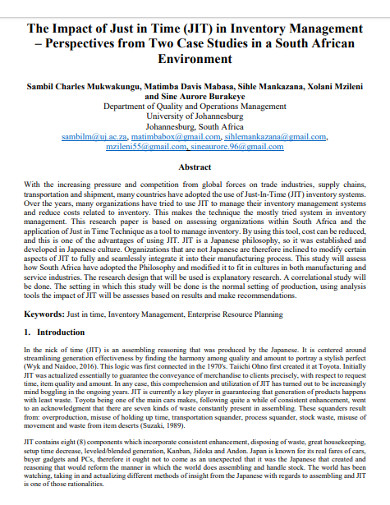
But waiting months to finalize one part design can set you back, and suddenly you’re in your product’s next model year and unable to deliver on your promised timeline. Issues crop up and you need to change the tool it’s not rare that molds require multiple iterations. You send the computer-assisted design (CAD) model abroad and wait, sometimes for months, to get the part back. Your company is ready to prototype a molded part design. Using fewer transfers to produce and deliver parts increases the chance that you’ll receive them when they’re needed. JIT suggests that working with local or regional - rather than global - suppliers can help simplify and improve the supply chain. So what can lessen these risks? A return to JIT sensibility, tied to Industry 4.0 principles.
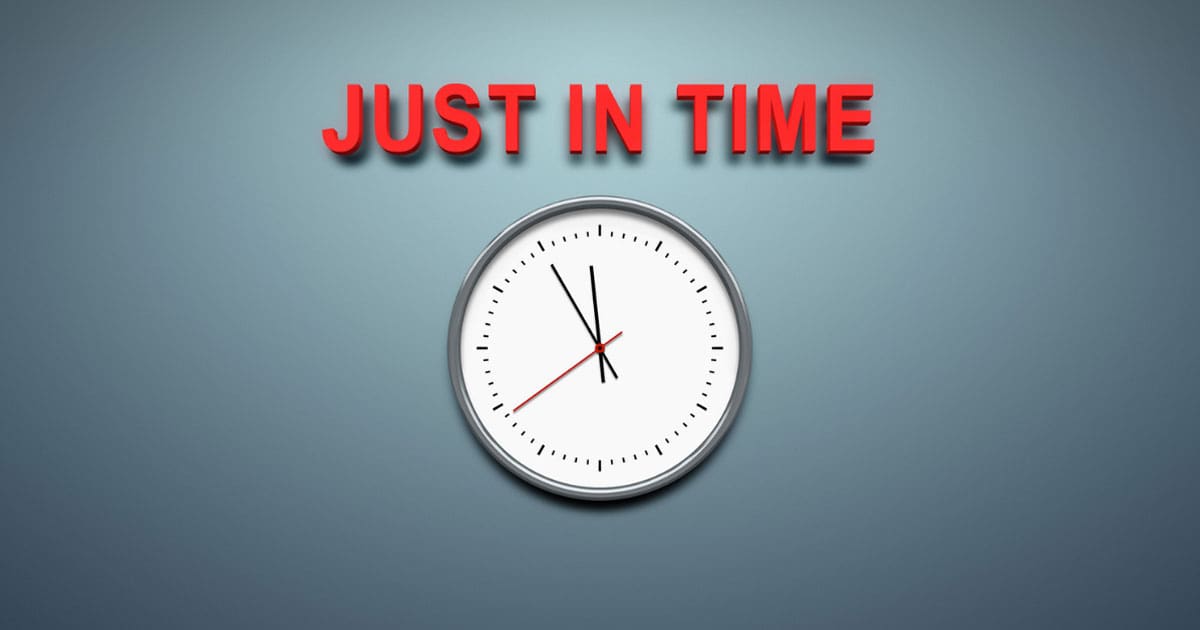
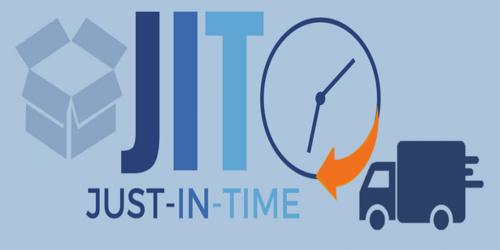
And of course, there’s the matter of tariffs. These one-time events seem to be happening with greater frequency, with pundits suggesting that instability is here to stay. They can also be affected by concerns such a pandemic, geopolitical upheaval, or even ships blocking international shipping lanes. It takes time to get parts produced and transported for inclusion in the final product, and even longer when they encounter international shipping and customs delays. Iteration across an ocean is a painfully slow process. If your parts speak to last year’s models and concepts more than this (or next) year’s, you may lose customers. Moreover, they want inventiveness and cutting-edge elements, especially advanced technology. Instead, consumers are looking for choice, uniqueness and customization. In today’s consumer culture, there’s an expectation that products don’t come in one flavor or style. There are also long-term costs incurred when your company can’t iterate quickly because of extended lead-times and excess inventory in the supply chain. In truth, however, it invites a litany of hidden costs to contend with, as entire supply chain organizations are needed to manage and move materials around the world. On the face of it, that move seemed smart, as it’s hard to beat piece-part pricing from certain foreign countries. As manufacturing globalized, the JIT methodology did as well, meaning that it became more typical to order parts in large quantities from abroad, then warehouse material to ensure it’s available when needed. Over time, however, the notion of having nearby suppliers providing “just-in-time” parts became something of a quaint relic. Finally, and most importantly, JIT reduces the need to warehouse inventory onsite, a hidden cost not usually considered when it comes to piece-part pricing from offshore manufacturers. You can even visit them, should you ever need to, enhancing your ability to maintain quality control.
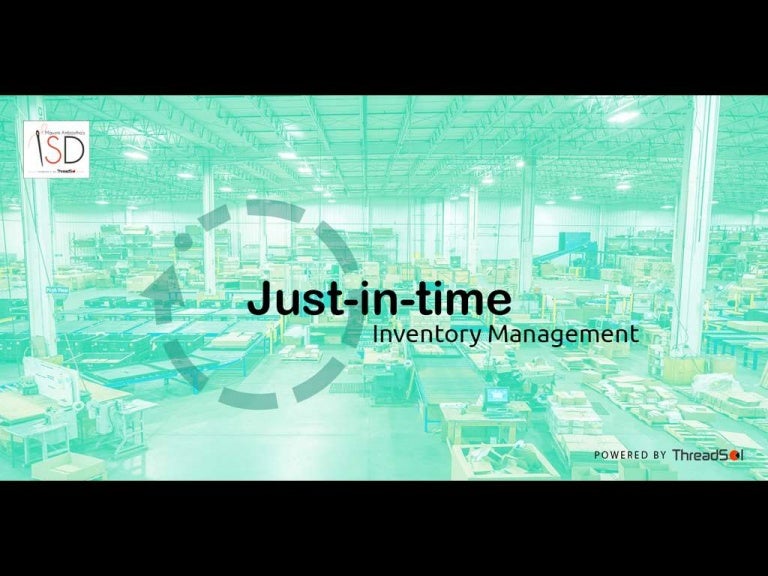
A side benefit is that local suppliers are more easily overseen. This lessens the time it takes to get parts to you, while massively reducing the cost of shipping. If you need more, recognize it in advance and order from a local supplier close to your company. Maintain just enough inventory onsite to keep the manufacturing supply chain humming for a given period of time. Given the automaker’s meteoric success over the past half-century, it can't be denied that JIT can be an incredibly effective system. Whether Toyota deserves the credit or not, it successfully applied it. The original JIT model was said to be perfected by Toyota as part of its Toyota Production System (TPS), although the company may have just been one of the first to apply the concept to manufacturing. Fifty years offers plenty of time and data to evaluate how the system has performed, how it’s changed, and specifically how it can be merged with Industry 4.0 principles to create maximum efficiencies. This was especially true during the supply chain crises of the past three years. In that time, however, the original concept has become muddied, causing some companies to face precisely the supply chain issues that JIT was conceived to solve. Just-in-time inventory management has been around for roughly half a century.
